When using precision rolling bearings, standardized installation of bearings is crucial in order to achieve maximum speed and lower temperature rise effects.
The installation of bearings should be carried out in a dry and dust-free area as much as possible, and should be kept away from equipment that may produce metal debris and dust. When it is necessary to install in complex environments, pollution should be minimized.
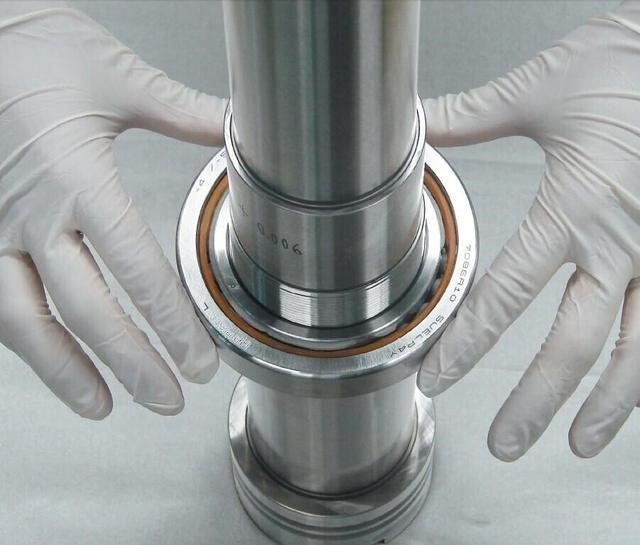
During the installation of bearings, there are steps such as cleaning, drying, (lubricating grease packaging) trial operation, assembly, etc., and all precautions should be followed.
Step 1: Clean the bearings and remove the rust proof oil.
Soak in highly volatile solvents such as refined kerosene and naphthol, and clean by hand. Remove the refined kerosene with gasoline, ethanol, etc. When using an air gun to blow off the cleaning oil, attention should be paid to the cleanliness of the air. When using oil and gas lubrication, it can be used directly, but it is recommended to apply or soak it in lubricating oil or low viscosity oil after cleaning.
Step 2: Dry the bearings to ensure there is no residual moisture.
When using grease lubrication, in order to prevent grease from flowing out, it is necessary to thoroughly dry the bearings. In addition, lubricating grease should be immediately sealed after drying. It can be dried with warm air (pay attention to the cleanliness of the air), or in a constant temperature bath.
In addition, due to the lubricating grease encapsulated inside the sealed bearing, it should not be cleaned and dried. The external rust proof oil should be wiped clean with a clean cloth before assembly.
Step 3: Seal the lubricating grease.
Ball bearings can be used with syringes and vinyl plastic bags aligned with the inner ring rolling surface, and lubricating grease can be evenly sealed between the balls. When there is a raceway guide cage, it is recommended to use small tools such as a spatula to apply it to the guide surface of the cage. If the inner space is narrow and it is not possible to seal the inner rolling surface, then seal the outer rolling surface. At this point, try to rotate it by hand to allow the grease to penetrate the inner ring.
When applying grease to the outer diameter surface (inner diameter surface) of the roller bearing, rotate the roller with your fingertips to allow the grease to seep into the inner ring (outer ring). After packaging, rotate the rolling part by hand to fully coat it with lubricating grease.
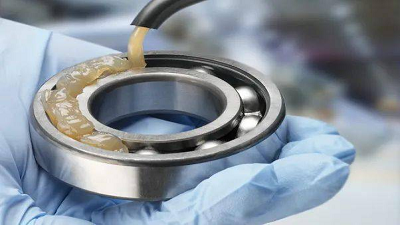
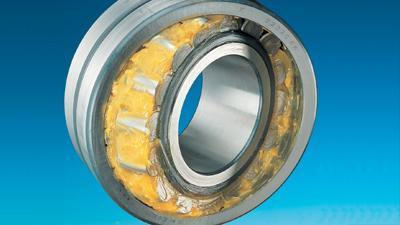
Step 4: Trial operation.
Ball bearings. It is recommended to increase the speed in units of 1000-2000 revolutions per minute after the temperature stabilizes. When the dmn (rolling element center diameter * speed) exceeds the range of 400000 times, for safety reasons, the speed should be increased in units of 500-1000 revolutions per minute.
Roller bearings. Compared with ball bearings, roller bearings have a longer peak temperature and a longer time to reach stable temperature during trial operation. In addition, due to the situation where the temperature rise caused by the re entanglement of lubricating grease cannot be stabilized, it should be operated for a long time at the highest speed. It is recommended to increase the speed in units of 500-1000 revolutions per minute until the temperature stabilizes. When the dmn (rolling element center diameter * speed) exceeds the range of 300000 times, for safety reasons, the speed should be increased in units of 300 revolutions.

Step 5: Assemble the bearings.
When installing bearings, mechanical, heating, or hydraulic methods should be selected based on the type and size.Regardless of the method used, it is necessary to reduce the impact of assembly and maintain the accuracy of bearings.
Firstly, Mechanical installation
When installing small bearings that are not too tight, you can use a sleeve and gently tap the sleeve with a hammer to install the bearing in the appropriate position. When striking, it should be applied evenly on the bearing ring as much as possible to prevent the bearing from tilting or tilting.
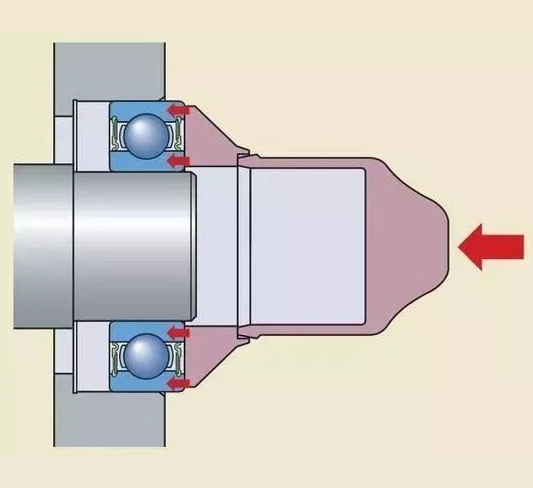
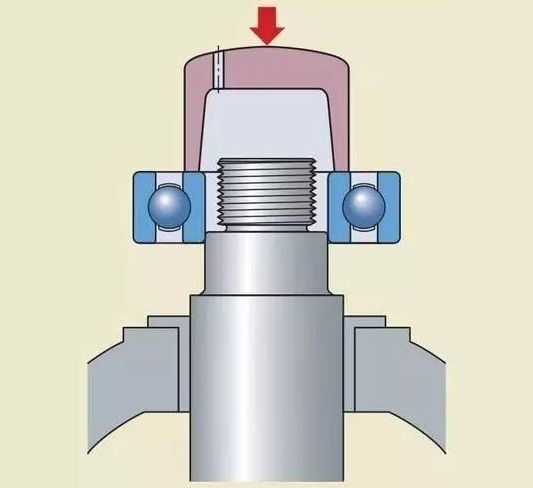
When assembling bearings on the spindle, there are usually two assembly methods for the inner ring of the shaft and bearing to be an interference fit (tight fit): hot insertion and hydraulic pressing.
Secondly, Hot installation
Usually, for the installation of larger bearings, it is impossible to do so without heating the bearings or bearing seats, as the force required for installation increases with the size. The temperature difference between the bearing ring and the shaft or bearing seat required for hot installation mainly depends on the interference and the diameter of the bearing fitting. The heating temperature of open bearings shall not exceed 120 ℃. It is not recommended to heat bearings with seals and dust covers above 80 ℃ (ensure that the temperature does not exceed the allowable temperature of the seals and lubricating grease). When heating the bearings, it is necessary to heat them evenly and there must be no localized overheating.
Thirdly, hydraulic press pressing in
Most bearings are installed using the pressing method. If the inner and outer rings of the bearing are to be installed on both the shaft and the bearing seat simultaneously, it must be ensured that the same pressure is applied to both the inner and outer rings, and the contact surface with the installation tool must be in the same plane.
When using a manual press to press in bearings, the first step is to calculate the pressure generated by the interference between the shaft and inner ring (a hydraulic press with a working pressure greater than the required pressure must be used). Then, when pressing in the inner ring, use the inner ring pressing tool to ensure that it is pressed into the shaft shoulder (do not apply force to the outer ring). After pressing in, measure the accuracy of each part of the bearing to confirm whether it is indeed installed on the shaft. In addition, when using multi row bearings for assembly, their runout should be measured after assembly to correct the axial deviation between the outer rings.
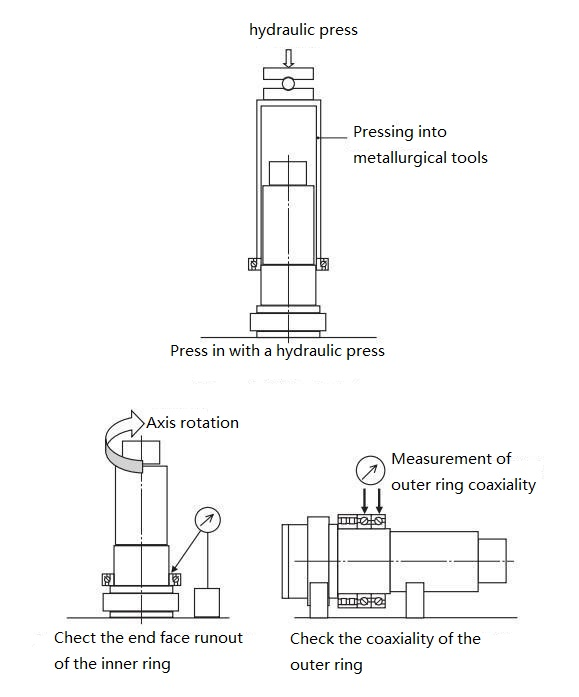
Post time: Dec-08-2023